При покупке бетоносмесительного устройства, в зависимости от компании, вам предлагают "бесплатный" бонус - набор готовых рецептур для производства бетона. Теоретически, вы их можете использовать - необходимо только обязательно скорректировать на местные заполнители. Практически же, вам скорее всего понадобится подбор состава под каждую номенклатуру бетонной смеси, которую вы планируете выпускать. В любом случае, в основе производства бетона будет лежать база данных рецептур - список массовых соотношений между компонентами бетона - песок (П), щебень (Щ), цемент (Ц), вода (В), добавка (Д) - для получения заданных свойств. На большинстве заводах рецептуры являются интеллектуальной собственностью и охраняются с особой тщательностью. Однако то, что рецептура долго используется, еще не означает, что возможности ее оптимизации исчерпаны. В общем случае, под оптимизацией рецептуры понимают такое ее изменение, которое обеспечивает более высокие показатели бетона при сохранении стоимости, либо уменьшение стоимости при сохранении нормируемых показателей.
В настоящее время тема снижения операционных расходов становится все более актуальней - рынок производителей бетонных смесей очень конкурентный и все производители отпускают бетон по более-менее одинаковой цене. Таким образом, играть на понижение цены у производителей нет возможности. Заработать на производстве бетона можно в двух случаях - 1) наличие государственного заказа, т.е. имеется гарантированный сбыт; 2) снижение операционных затрат. Снижение, например, расхода цемента в рецептуре с 380 до 370 кг/м3 (10 кг на 1 м3) при суточном объеме производства в 100-200 м3 бетона приведет к снижению затрат около 2 млн. рублей в год.
Рассмотрим один из возможных путей оптимизации рецептуры. На рисунке 1 показаны значения прочности бетона за период наблюдений 2 месяца на одном из заводов - график колебаний прочности. Рецептура неоптимизированная.
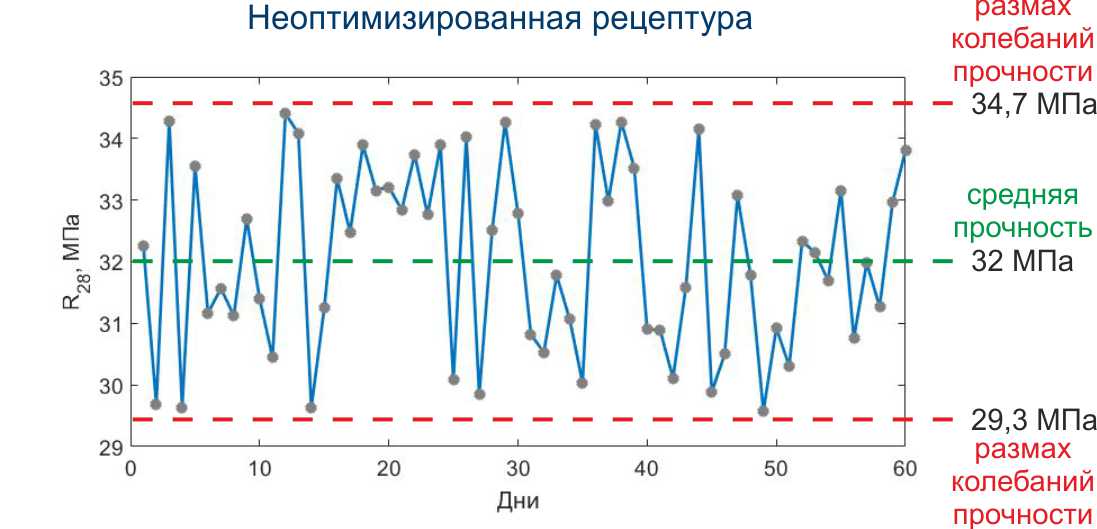
График показывает, что все значения прочности колеблются относительно одного среднего значения - 32 МПа. При этом максимальные отклонения от этого значения составляют плюс-минус 2,7 МПа. Обычно такой статистический разброс характеризуется коэффициентом вариации, но в данном случае мы ограничимся величиной, которая называется размахом. Итак, для неоптимизированной рецептуры размах составляет 5,4 МПа. Сама рецептура следующая - Ц - 398 кг, П - 627 кг, Щ - 1192 кг, В - 172 л, Д - 4,0 кг. Обратите внимание, что самыми сильными факторами являются активность цемента, водоцементное отношение и упаковка зерен заполнителей, которая зависит от гранулометрического состава.
Рецептура на рисунке 1 подбиралась с целью обеспечения заданного класса бетона - для компенсации большого размаха в бетон добавляют больше цемента. Таким образом, уменьшая размах колебаний прочности мы можем несколько снизить расход цемента. Этот же принцип лежит в основе стабилизации прочности. В случае, если нестабильность прочности вызвана колебаниями активности цемента, размах колебаний можно эффективно уменьшить за счет правильно подобранной упаковки заполнителей. Упаковка подбирается с помощью варьирования соотношения долей песка и щебня в составе бетонной смеси. Механизм стабилизации характеристик более подробно рассмотрен в разделе - Стабилизация прочности - уменьшение ее разброса. На рисунке 2 приведены данные по измененной рецептуре, в которой упаковка заполнителей подобрана таким образом, чтобы минизировать размах колебаний - с 5,4 МПа до 3,4 МПа.

Рецептура, обеспечивающая меньший размах колебаний прочности, вследствие измененной упаковки заполнителей получилась следующая - Ц - 391 кг, П - 607 кг, Щ - 1217 кг, В - 169 л, Д - 3,9 кг. Как видим, расход цемента уменьшился на 7 кг. Уменьшение связано с тем, что мы добавили больше крупной фракции и новая упаковка заполнителей уменьшила роль цементного камня в распределении внешней нагрузки. Нагрузка на зерна щебня при этом увеличивается, однако их прочность более стабильная и имеет более высокое значение, чем прочность цементного камня. Таким образом, новая упаковка обеспечивает более экономный состав бетона. Водоцементное отношение осталось прежним, однако изменилось количество воды, что, как кажется, должно вызвать уменьшение осадки конуса. Этого не происходит, так как часть песка, который также влияет на подвижность смеси (при более высоком содержании песка, смесь менее подвижна), была удалена из рецептуры, тем самым компенсируя недостаток воды. Как результат - бетонная смесь и бетон по своим показателям (осадка конуса и прочность) не изменились, однако цемента требуется меньше
Следующий путь оптимизации рецептуры продемонстрирован на рисунке 3, где показаны данные по измененной рецептуре, однако с другой упаковкой. Новая упаковка заполнителей подобрана таким образом, чтобы поднять среднее значение прочности бетона, при этом размах колебаний не интересовал.
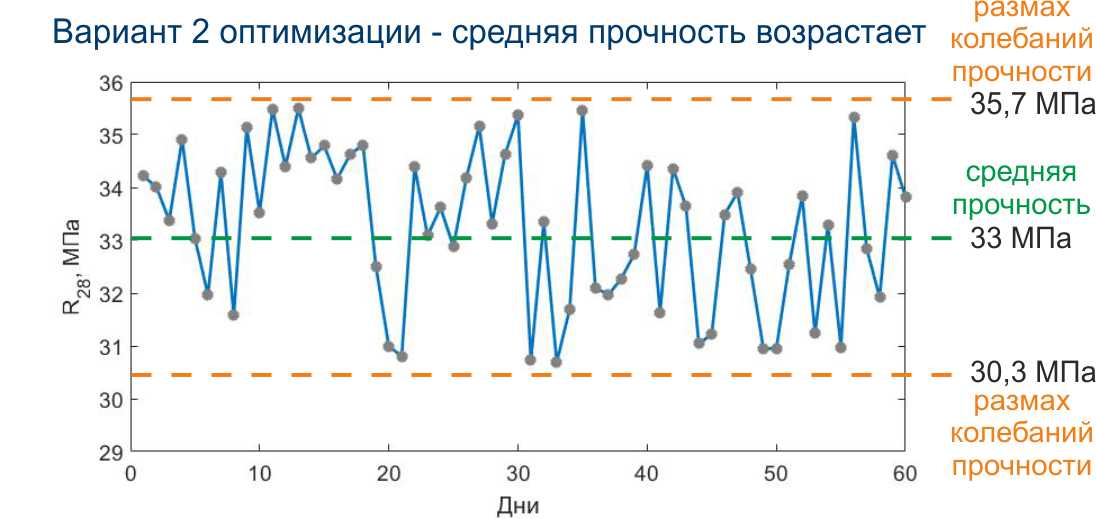
Получившаяся рецептура имеет следующий вид - Ц - 395 кг, П - 635 кг, Щ - 1180 кг, В - 171 л, Д - 4,0 кг. Для увеличения прочности на 1 МПа было найдено соотношение заполнителей, обеспечивающее более плотную их упаковку в составе смеси, что позволило сократить расход цемента за счет уменьшения пустотности. Возрастание прочности связано с тем, нагрузка стала распределятся в большую сторону на заполнители, которые прочнее цементного камня. Недостатком данной рецептуры является то, что она становится менее подвижной - осадка конуса в среднем уменьшается на 1-2 см. Это уменьшение можно компенировать с помощью более длительного воздействия на смесь вибрирующих элементов на этапе уплотнения смеси.
И наконец, как оказалось самая эффективная упаковка в данном случае позволяет одновременно как увеличить среднюю прочность бетона, так и уменьшить размах ее колебаний, что показано на рисунке 4.
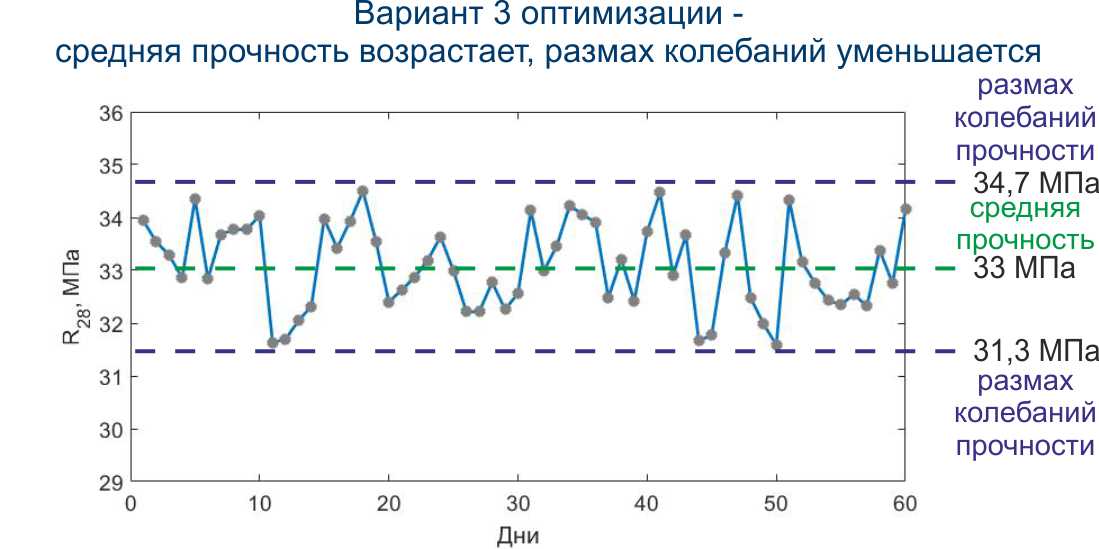
Получившаяся рецептура имеет следующий вид - Ц - 386 кг, П - 585 кг, Щ - 1259 кг, В - 167 л, Д - 3,9 кг. Отличием данной рецептуры от предыдущих является учет, помимо пустотности заполнителей, также и их полной поверхности. Цементный гель расходуется на заполнение пустот в заполнителе и формирование тонкой пленки, обвалакивающей каждое зерно заполнителя. Убрав часть песка, в новой рецептуре была уменьшена полная поверхность, и, хотя пустотность смеси возрасла, часть излишка цементного геля, ранее уходившего на формирование пленки, теперь заполнила добавочную пустотность, а другая часть оказалась ненужной и ее можно убрать из состава. Новая рецептура увеличила среднее значение прочности на 1 МПа, что дало в итоге 33 МПа, а размах колебаний уменьшился до 3,4 МПа. Экономия цемента по сравнению с первоначальной рецептурой за счет правильно подобранной упаковки заполнителей составила 12 кг.